NDT Inspection Services
Sutro offer a comprehensive
range of industry-proven
specialist NDT inspection services
NDT Inspection Cardiff
As the name suggests Non-Destructive Testing (NDT) is a method for testing and analysing industrial components and materials without damaging them. A visual inspection using the naked eye is the most basic form of NDT. Other NDT methods make use of sound, radio waves and electromagnetic energy to examine everything from industrial hardware to oil & gas infrastructure to power pylons and wind turbines.
The purpose of NDT is to inspect vital industrial components in a safe, accurate and cost-effective way that minimises the disruption to your business by avoiding plant closures and downtime.
What are the benefits of NDT?
The main benefit of NDT is the fact that the component being tested is not damaged as part of the process which means that it can be repaired rather than replaced. Other benefits include:
Our NDT applications
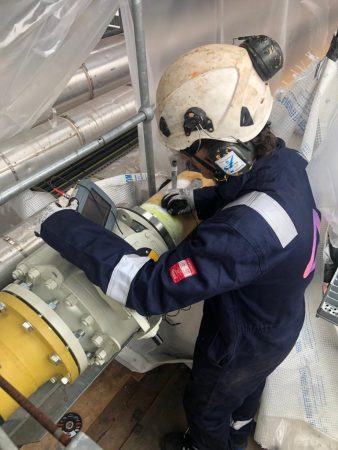
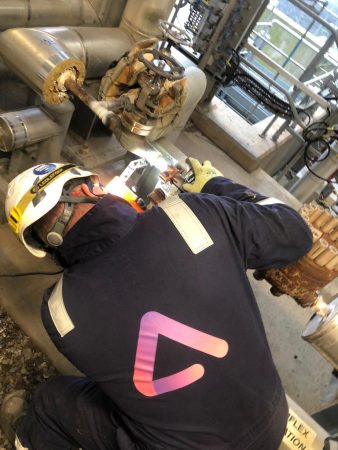
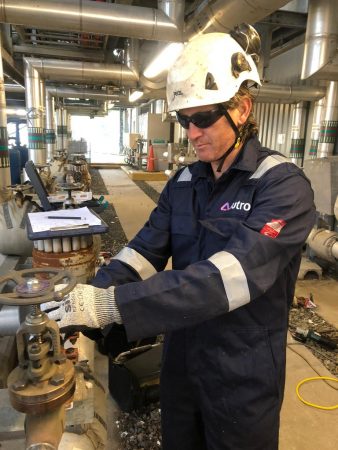
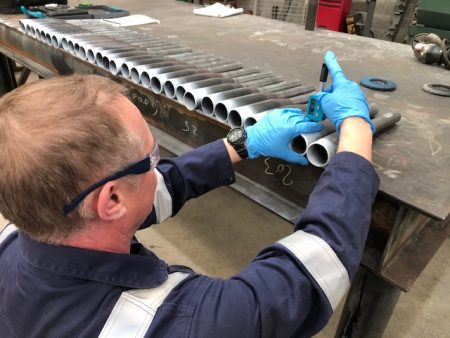
Which industries use NDT?
Sutro works with a broad range of industries that require NDT inspections and surveys. Many of our clients adhere to formal inspection procedures while others use non-destructive testing as part of routine maintenance. Industries include:
- Power generation
- Offshore oil & gas
- Green energy – wind and solar
- Civil engineering – roads, bridges and rail infrastructure
A common application is to test quality control standards, for example, testing welds and welding procedures to ensure that they are compliant with the correct specifications.

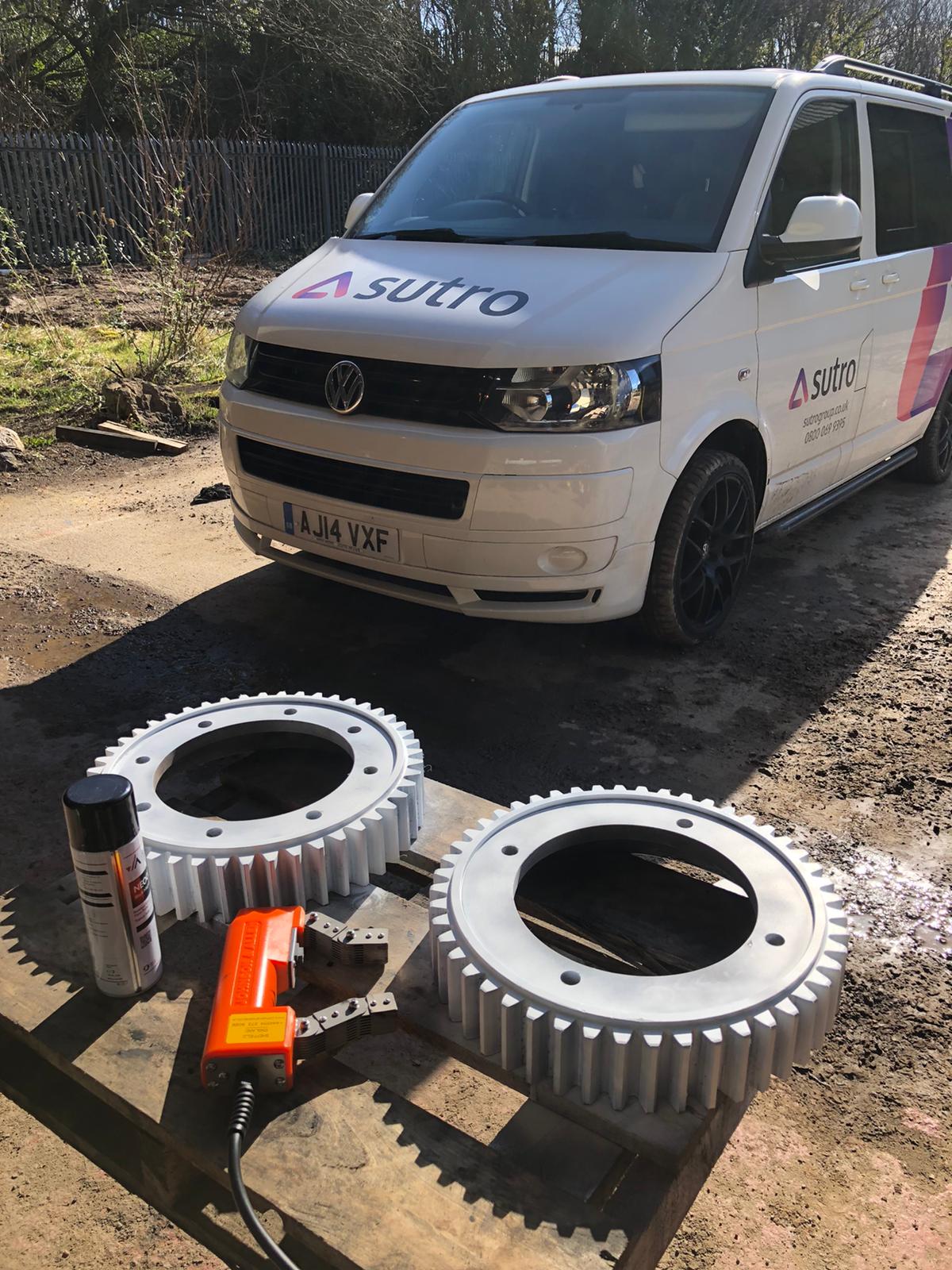
Why choose Sutro Group for NDT inspections?
Our NDT Inspection Engineers are fully equipped and capable of delivering the testing solutions your industry requires. Sutro engineers have over 25 years of experience working with industry leaders across the industrial, construction, power, utilities, oil, gas and green energy sectors.
Whether its dye penetrant, magnetic particle or ultrasonic testing, our service capabilities make us the ideal ‘one-source’ provider for monitoring and inspection solutions.
Adopting this ‘one-source’ approach, eliminates the necessity for multiple contractors and associated costs, allowing our clients to be as efficient as possible – ultimately increasing productivity and reducing costs for our customers.
We have operating centres in Cardiff and Newport in South Wales, Corston in South West England and Gdańsk in Poland. This enables Sutro to operate drone inspection services for our clients throughout the UK and Europe we can quickly mobilise our ISO certified team of inspection engineers for the most complex NDT projects.
Latest NDT Inspections blog posts
Contact us to arrange a site survey, specific to
your maintenance requirements.
Find out how our access solutions can offer you cost efficiency whilst ensuring quality and safety.
0800 069 9395
Frazer Building
126 Bute Street
Cardiff
CF10 5LE